Wastewater Treatment Plant Studied by EPA for Innovation
The Hillsborough Wastewater Treatment Plant is getting some attention due to its innovative work in treating wastewater.
The plant was one of five in the United States and one in Canada to be selected by the Environmental Protection Agency for case studies on innovative technologies to significantly intensify treatment or improve removal of the nutrients nitrogen or phosphorus.
The South Durham Water Reclamation Facility in Durham also was selected, along with facilities in Buford, Georgia; Kingsley, Iowa; Alexandria, Virginia; and British Columbia.
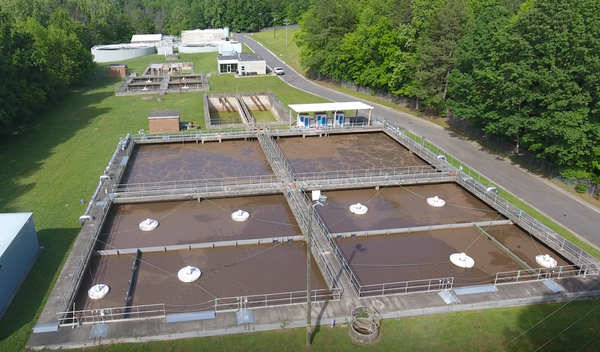
Over 36 months, the EPA Office of Wastewater Management analyzed the long-term performance of the facilities, using data provided by the facilities on operational processes and final effluent, treated wastewater.
The EPA is sharing the information from the study with other municipal facilities through the document “Innovative Nutrient Removal Technologies: Case Studies of Intensified or Enhanced Treatment,” published last fall, and a webinar now being offered.
“I think it’s super cool that our plant’s successes were selected by the EPA to be highlighted along with only four other plants in the nation,” Hillsborough Wastewater Treatment Plant Superintendent Jeff Mahagan said.
The Hillsborough plant was selected for its low nitrogen biological nutrient removal enhancement modification that was added with its Phase 1 upgrades, completed in 2014. The upgrades were required to meet state requirements for the protection and restoration of Falls Lake, which is on the EPA’s list of impaired waters and is where Hillsborough’s watershed drains. Those requirements reduced Hillsborough’s total nitrogen discharge to 10,422 pounds annually, beginning in 2016. The discharge limits were believed to be the strictest across the nation at that time.
Hillsborough staff modified the nutrient removal upgrades to meet the discharge limits without including reverse osmosis or ion exchange processes or adding carbon or other chemicals to the plant. Their modifications delayed further upgrades to the plant that will be needed for further restrictions and reduced the upgrade’s cost, originally estimated at $30 million. By redesigning and building some of the upgrades on their own, staff reduced the Phase 1 cost to about $19 million.